OSHA’s Top 10 violations: three action steps for employers
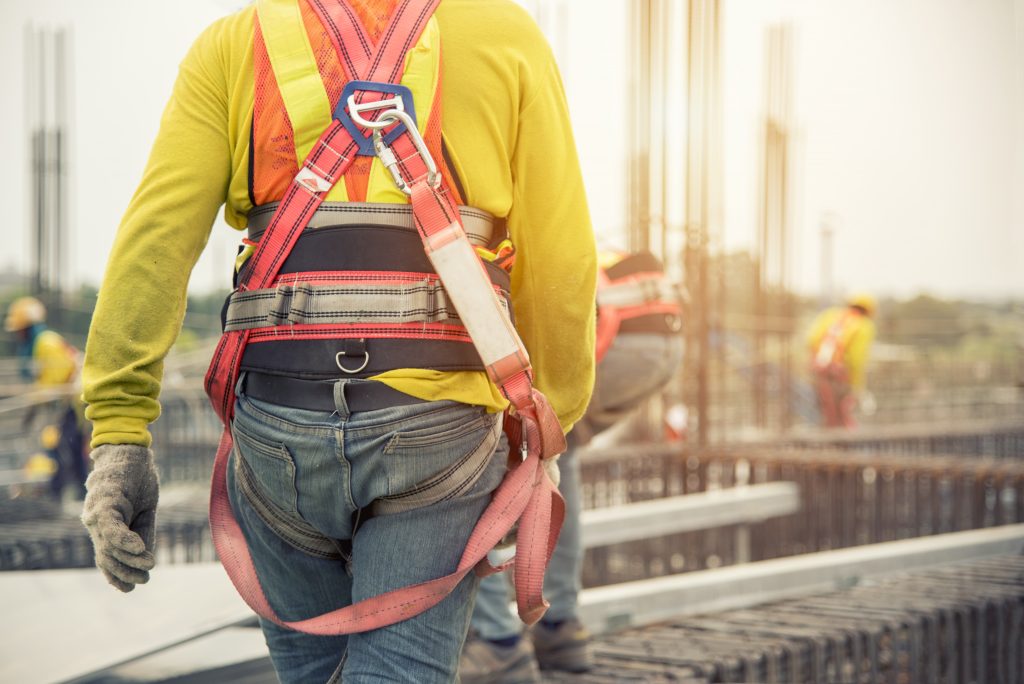
For the ninth consecutive year, Fall Protection – General Requirements is the most frequently cited standard, OSHA announced at the 2019 National Safety Council Congress & Expo. The rest of the preliminary list of the Top 10 violations for fiscal year 2019 also remained largely unchanged from FY 2018, with one minor change. Lockout/Tagout, which ranked fifth in FY 2018, advanced to No. 4, trading places with Respiratory Protection. The data, which covers violations cited from October 1, 2018 through August 31, 2019, is preliminary, and therefore, the numbers may change. However, the ranking is likely to remain consistent when the final numbers are released later this year.
Here are the top 10 violations:
1. Fall Protection (construction) – General Requirements (1926.501) – 6,010 violations
Common violations included failure to provide fall protection near unprotected sides or edges and on both low-slope and steep roofs. Roofing, framing, masonry and new single-family housing construction contractors were among the most frequently cited. Although the fall protection standard was updated in 2016, some experts suggest it will take several years for employers to get the necessary facility updates into their budgetary cycle.
2. Hazard Communication (1910.1200) – 3,671 violations
Considered low-hanging fruit for inspectors, hazard communication has been #2 for several years. Lack of a written program, inadequate training, and failure to properly develop or maintain safety data sheets (SDSs) are common citations. Auto repair facilities and painting contractors were among the industries that received many hazard communication citations.
3. Scaffolding (construction) – General Requirements (1926.451) – 2, 813 violations
Masonry, siding, and framing contractors are the most commonly cited employers for this violation. Lack of proper decking, failure to provide guardrails where required, and failure to ensure that scaffolds are adequately supported on a solid foundation are common violations.
4. Lockout/Tagout (1910.147) – 2, 606 violations
Employers cited under this standard failed to establish an energy control procedure, did not train employees in proper lockout/tagout procedures, failed to conduct periodic evaluations of procedures, and failed to use lockout/tagout devices or equipment. Plastics manufacturers, machine shops, and sawmills were frequently cited.
5. Respiratory protection (29 CFR 1910.134) – 2,450 violations
Citations related to failure to fit test, establish a program, and medically evaluate employees who wore respirators were common violations issued. Auto body refinishing, painting contractors, masonry contractors, and wall covering contractors received many citations.
6. Ladders (construction) (1926.1053) – 2,345 violations
Ladders continued to be a common violation in the roofing, siding, framing and painting trades. Frequent violations include, ladders with structural defects, failure to have siderails extend three feet beyond a landing surface, using ladders for unintended purposes, using the top rung of a step ladder, and ladders with structural defects.
7. Powered Industrial Trucks (1910.178) – 2,093 violations
Forklift violations dominated this standard, including deficient or damaged forklifts that were not removed from service, failure to safely operate a forklift, operators who had not been trained or certified to operate a forklift, and failure to recertify forklift drivers and evaluate every three years. Violations were widespread across many industries, but particularly prominent in warehousing and storage facilities and fabricated and structural metal manufacturing.
8. Fall Protection (construction)– Training Requirements (1926.503) – 1,773 violations
Violations of this standard include failing to provide training to each person required to receive it, failure to certify training in writing, inadequacies in training leading to the failure of retention by the trainee, and failing to retrain in instances where the trainee failed to retain the training content.
9. Machine Guarding (1910.212) – 1,743 violations
While cited in many industries, machine shops and fabricated metal manufacturing saw many citations for failing to ensure that guards are securely attached to machinery, improper guarding of fan blades, and failure to properly anchor fixed machinery.
10. Personal protective and lifesaving equipment (construction)—eye and face protection (29 CFR 1926.102) – 1,411
Appearing on the list for the first time IN FY 2018, this standard includes failing to provide eye and face protection where employees are exposed to hazards from flying objects, failing to provide protection from caustic hazards, gases, and vapors, and failing to provide eye protection with side protection. Violations were concentrated in the housing industry, with roofers, house framers and other contractors cited often.
Three action steps for employers
With little variation from year-to-year, this list is a reminder to employers that the same violations are putting employees at risk and costing employers thousands of dollars in citations. Here are three steps to take:
1. Drill down to your industry
Employers can drill down even further and look at the most frequently cited Federal or State OSHA standards by industryhttps://www.osha.gov/pls/imis/citedstandard.html for a specified 6-digit North American Industry Classification System (NAICS) code. If your facility is inspected, there’s a very good chance it will include these issues.
2. Be strategic
A common approach is to conduct walk throughs, which can be helpful to identify new or previously missed hazards and failures in hazard controls. However, this is reactionary, not strategic. OSHA states, “an effective occupational safety and health program will include the following four main elements: management commitment and employee involvement, worksite analysis, hazard prevention and control, and safety and health training.” Having a risk management approach is the best possible defense.
3. Continually reinforce training and commitment to safety
Learning does not start and stop with training, safe practices have to be practiced and applied to be lasting. While most workers know not to stand on the top rung of a step ladder, it happens because they are in a hurry, careless, or not paying attention. Signage, toolbox talks, digital reminders all help; but most important is effective leadership and employee engagement. When managers enforce the safety rules and stand behind them 100%, workers understand it’s important to their health and well-being and are empowered to take ownership of their own and other’s safety.
Further, employee complaints triggered 41% of the unprogrammed inspections and over 23% of all inspections. Employees who feel safe at work and believe the employer cares about their safety, are less likely to file a complaint.